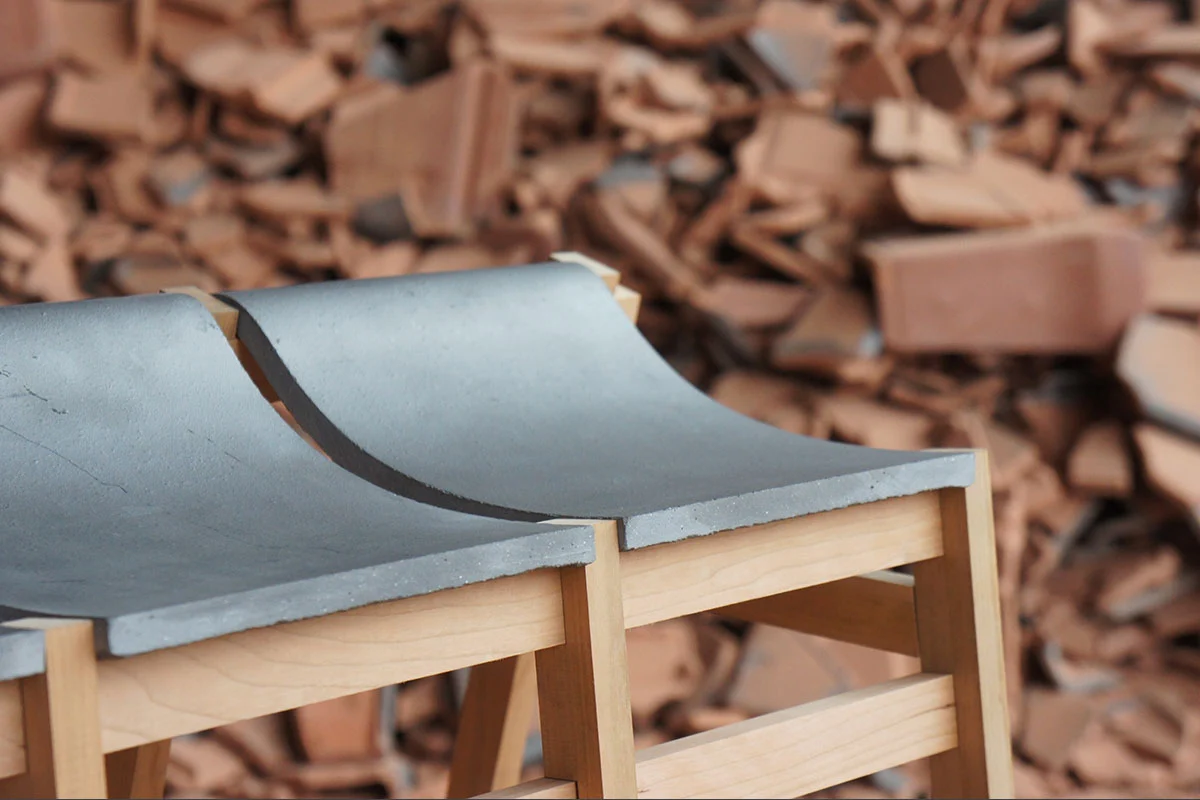
Industrija građevinskih, oblagajućih i dekorativnih materijala je nepresušni izvor inovacija. Ali ma koliko se na tržištu podnih i zidnih obloga stalno pojavljivalo nešto novo, interesantno je da uvek postoji određena grupa materijala koji definitivno nikada “ne izlaze iz mode” i koje slobodno možemo nazvati trajno aktuelnim. U tu grupu bez sumnje spada jedan od najstarijih dekorativnih materijala na svetu – keramika.
Keramika je jako dugo, vekovima unazad, obrađivana na starinski način, koji je u doba neolita podrazumevao pečenje gline u jamama u zemlji, a kasnije u pećima konstruisanim specijalno za ove svrhe. Poznato je da, od trenutka kada se oblikuje, jedna keramička pločica mora da prođe dve faze pečenja na različitim temperaturama i proces glaziranja, kako bismo mogli da dobijemo podnu ili zidnu oblogu spremnu za upotrebu.
Najozbiljniji “igrači”
Taj princip se nije promenio sve do danas, ali su u njega vremenom uključene određene tehnološke novine, zahvaljujući kojima je moguće dobiti otporniju i bolju keramiku nego ikada pre. U konstruisanju najsavremenijih peći i osmišljavanju novih metoda obrade u svetu prednjače Italijani, ostavljajući iza sebe Španiju, SAD i neke orijentalne zemlje, kao najozbiljnije “igrače” na tržištu keramike.
Tehnologija proizvodnje keramike zapravo je deo tehnologije silikatnih proizvoda, koja još uključuje proizvodnju vatrostalnih materijala i stakla. Pojednostavljeno sagledano, proizvodni ciklus keramike odvija se u pet faza. Polazna tačka je priprema sirovina (uključuje obogaćivanje polaznih sirovina, toplotnu obradu i mlevenje sirovina), sledi priprema keramičke mase (podrazumeva mešanje sirovina, dodavanje veziva i vakumiranje mase), oblikovanje, sušenje i na kraju pečenje finalnog proizvoda, na kom se po potrebi mogu vršiti neke dodatne operacije.
CILJ FAZE PRIPREME SIROVINA jeste modifikacija njihovog hemijsko-minerološkog sastava i obezbeđivanje potrebnog stepena čistoće, postizanje odgovarajuće veličine čestica i stepena vlage, neophodnog za dalju obradu.
Kada govorimo o obogaćivanju, taj deo procesa odnosi se na mehaničku pripremu ispiranjem vodom i separacijom čestica na specijalnim sitima, a zatim i na hemijsko prečišćavanje, te sušenje i sitnjenje čestica. Takozvanu klasičnu, odnosno silikatnu keramiku dobijamo od minerala feldspata, kvarcnog peska i različitih vrsta gline, a konkretno dekorativnu keramiku koja je trenutno predmet našeg interesovanja, od najkvalitetnijih među njima.
GLINE su sedimentne stene u čiji sastav ulaze minerali, među kojima kao najvažniji kaolinit, montmorilonit (hidratisani silikat aluminijuma i magnezijuma) i ilit (hidratisani silikat kalijuma, aluminijuma i magnezijuma).
Minerali iz grupe feldspata takođe su alumoslikati, čijim prirodnim razlaganjem nastaje kaolinit i sam mineral bele boje, najvišeg stepena čistoće i kvaliteta, od kog se dobija porcelan. Sjedinjavanjem svih sirovina u homogenu smešu dobijamo keramičku masu. Određene sirovine među prethodno pomenutim mogu imati posebnu ulogu u procesu proizvodnje keramike, prema kojoj se dele na plastifikatore, opošćivače i topitelje.
Plastifikatori omogućavaju oblikovanje i tu spadaju gline i njihovi minerali.
Opošćivači smanjuju skupljanje keramičke mase prilikom sušenja i pečenja (kvarc, pesak, šamot), a zadatak topitelja je snižavanje temperature pečenja kako ne bi došlo do pucanja keramike (feldspat).
Mešanje sirovina kao deo pripreme keramičke mase podrazumeva dovođenje njihovog sastava u homogeno stanje, doziranjem sastojaka u odgovarajućoj masenoj i zapreminskoj proporciji, u specijalnim mešalicama i potonjim filtriranjem smeše. U zavisnosti od agregatnog stanja sirovina razlikujemo suvo i mokro mešanje. U dalekoj prošlosti keramičke pločice oblikovane su ručno i samim tim imale neravnu površinu, sve dok nisu napravljene prve mehaničke prese koje su funkcionisale po principu stege. Oblikovanje keramike danas se vrši mašinskim presovanjem praškaste keramičke mase koja sadrži od 3% do 10% vode, pod visokim pritiskom ili ekstrudiranjem odnosno istiskivanjem kroz kalup.
Keramika se nadalje podvrgava sušenju u takozvanim kanalnim sušarama, na vazduhu sa određenim udelom vodene pare, kako bi se smanjio procenat vode u keramičkoj masi na nivo koji neće ometati kasnije proces pečenja. Početna temperatura sušenja se kreće između 30 i 40 stepeni, da bi se kasnije, kada operacija stigne do polovine ciklusa, procenat vlage smanjio, a temperatura u sušari povećala na 80 stepeni. Kada se keramika ohladi od sušenja sledi pečenje. U ovoj, poslednjoj fazi obrade, keramika trpi brojne fizičko-hemijske promene, koje dolaze kao posledica procesa sinterovanja.
Često se dešava da prodavci u salonima upotrebljavaju izraz sinter pločice prilikom opisivanja proizvoda, a da pritom sami ne umeju kupcu da objasne šta to tačno znači i zašto bi trebalo da se odluči baš za te pločice.
Sinterovanje predstavlja fizički proces smanjivanja rastojanja između čestica pod uticajem visoke temperature i posledično dodatno sabijanje keramičkog proizvoda. Kao rezultat ovog procesa dobijamo čvršću keramiku smanjenih dimenzija i povećane gustine, a stepen sinterovanja zavisiće od temperature, vremena pečenja i intenziteta pritiska u peći.
OSNOVNA PODELA KERAMIČKIH PROIZVODA je upravo na sinterovane i nesinterovane, gde u prvu grupu spadaju porcelan i dekorativna keramika, a u drugu luksuzne italijanske pločice izrađene po starinskoj metodi kao što je fajans i majolika i građevinska keramika (cigla i crep).
Zaključak je, dakle, da je sva podna i zidna keramika koju možete naći u prodaji sinterovana, te da taj detalj ne predstavlja nikakav dodatni kvalitet zbog kog bi neka vrsta pločica trebalo da bude skuplja u odnosu na neku drugu. Keramika se peče u tunelskim pećima, u kojima, krećući se po pokretnoj traci, prvo ide na predgrevanje, zatim glavno pečenje na temperaturi od 950 pa sve do 1300 stepeni (zavisno od tipa pločica koje hoćemo da dobijemo) i na kraju na hlađenje. Kada prođe kroz sve faze obrade, keramika se na kraju može još i glazirati radi dobijanja glatke, sjajne površine. Glaziranje se vrši prskanjem, umakanjem pločica u glazuru ili prolaskom pločica kroz „zavesu“ od suspenzije glazure, a svrha glaziranja je poboljšavanje opšteg vizuelnog utiska finalnog proizvoda.
Keramika – osnovna podela
Nisu, međutim, sve pločice obavezno glazirane. Načelno postoje četiri velike grupe u koje možemo razvrstati keramičke pločice, rukovođeni temperaturom pečenja, brojem pečenja, faktorom glaziranosti, procentom upijanja vode tj. poroznošću i, na kraju, namenom.
Earthenware
Prva grupa su earthenware pločice ili žargonski grnčarija. To su glazirane zidne pločice sa procentom upijanja vode preko 10%, namenjene unutrašnjoj upotrebi. Male su mase, krte i visoko porozne, a u zavisnosti od broja pečenja nose oznaku monoporosa ili biporosa. Peku se u intervalu između 950 i 1150 stepeni Celzijusa, što će zavisiti od toga da li se glazura aplicira tokom pečenja osnove (monoporosa), ili će se podvrgnuti još jednom pečenju kako bi im se dodala dekorativna aplikacija. Mogu biti mat ili sjajne, oborenih ili ivica naknadno sečenih pod pravim uglom (rettificato).
Monocottura
Druga grupa pločica definiše pločice koje se izrađuju od tela pločice tamno crvene boje, popularno nazvane monocottura u koje spadaju najčešće španske zidne, ali i neke podne keramičke pločice čije telo pločica najčešće podseča na ciglu i/ili crep, pa kao takav materijal ima svojstvo upijanja vlage od 3-0,5% što daje mogućnost za proizvodnju nešto čvršćih zidnih i podnih pločica koje se mogu primenjivati samo u unutrašnjem polaganju, jer ovaj tip keramike nema izražen faktor mrazootpronosti koji je neophodan za spoljno polaganje. Peku se u intervalu između 950 i 1150 stepeni Celzijusa, što zavisi od željenog tipa površine i primene.
Fine porcelain stoneware
Treća grupa su fine porcelain stoneware, iliti grupa glaziranih porcelana. One su tvrđe i otpornije od prve grupe i uglavnom ih čini program podnih obloga. Uglavnom su glazirane, peku se na temperaturi od 1200 pa do 1400 stepeni, a kako im je upijanje vode manje od 0,5% mogu se koristiti i unutra i spolja. Imaju znatno veću masu, te tako jedan kvadrat ovih pločica može težiti i do 20kg, a mogu biti mat, reljefne i protivklizne varijabilnog stepena.
Izuzetno čvrsta glazura nastala zastaklivanjem mase tela pločice i slojeva osnovnih, ali i završnih glazura sa aplikacijama koje se nanose na površinu pre pečenja omogućava primenu dodatnih efekata obrade površine, pa mogu biti polirane (levigato), polu-polirane (lappato), ali dodatno obrađenih ivica (rettificato). Izuzetno su otporne na termo šokove, kao i na uticaj mehaničkih oštećenja na glaziranu površinu.
Pošto je Italija neprikosnovena domovina vrhunske keramike, svojstva pločica uglavnom nose italijanske nazive, a oznaka ove grupe je porcellanato smaltato, odnosno upravo glazirani porcelan, a ovu vrstu keramike proizvode i domaće fabrike.
Porcelain stoneware & full body
Poslednju, a ujedno i najusavršeniju grupu, čine porcelain stoneware i full body – neglazirane, visokootporne „kamenite“ pločice. Peku se na najvišoj temperaturi od 1300 stepeni, a procenat upijanja vode im iznosi manje od 0,5%, za šta treba zahvaliti upravo toj temperaturi i sastavu keramičke mase, koji uključuje minerale koji ulaze u sastav granita, zbog čega ih često zovu granitnom keramikom. Jako su otporne, kako na mehanička oštećenja odnosno ogrebotine, tako i na određene hemikalije. Kod ovih pločica boja lica je ista kao i boja naličja i na njima je moguća izrada aplikacija u visokoj rezoluciji, odnosno imitacija brojnih reljefastih šara do poslednjeg detalja.
Odsustvo glazure čini ih pogodnim za obradu posle pečenja, u smislu poliranja, polu-poliranja, sečenja ivica i izrade oborenih ivica.
Stoga iz ove grupe imamo mat, reljefne, polirane (levigato), polu-polirane (lappato), pravilno reljefne (strutturato) i reljefno-protivklizne pločice (bocciardato).
One koje nose oznaku naturale nisu prošle nikakvu obradu. U našoj zemlji još uvek nema proizvođača koji ima resurse za pravljenje ove vrste keramike, zbog kalibra investicije u najsavremenije peći i mašine za obradu, koji srpski proizvođači još uvek ne mogu da dostignu, pa se stoga ista može nabaviti samo iz uvoza, uz konstataciju da kvalitet prati i primetno visoka cena.
Autor teksta: Jelena Mitrović, diplomirani novinar